

Wood is a pretty poor insulator, and when you construct a traditional wall, you usually have studs spaced every 16 to 24 inches. Building with SIPs eliminates the need for studs and framing, which results in more efficient walls. They can be challenging to modify after they leave the factory, so designers and builders usually work within the parameters of the standard sizes - like constructing with blocks.įor those who are interested in engineering, SIPs are a fascinating option - a material created by modern technology. Prefab SIPs come in various sizes, but most are between 4×8 feet and 8×24 feet. SIP panels are highly engineered products that are almost always created in a factory setting using machines to apply glue and pressure to bond the SIP together and cure just right. Others may use outer layers of plywood, fiber cement, gypsum, or even metal. Some use other insulators like polyurethane. Now, not all SIPs are made from OSB and polystyrene. These layers are bonded together to create rigid four to 12-inch thick prefabricated panels that make excellent building materials for tiny homes. The “cookie” layer is comprised of OSB (oriented strand board) and the inner “ice cream” layer is made of expanded polystyrene foam. Why? Because that’s exactly what these structural insulated panels look like.
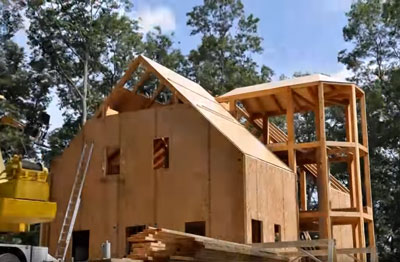
I must admit that researching SIPs left me craving an ice cream sandwich.
#A frame sip house how to#
What Are SIPs Pros and Cons Cost of Using SIPs How To Build With SIPs How To Install SIPs
